Thermal Products
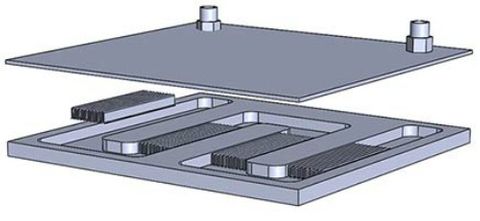
Friction Stir Welding Solutions for the Thermal Industry
HFW Solutions has worked with thermal industry companies to develop and create new and innovative parts and solutions that are stronger, lighter, hermetically sealed, and more reliable. Our thermal industries solutions include making our products from extrusions or castings. We understand the complexities of planning for the inevitable change within the thermal industry and the critical need for solutions that can adapt over time.
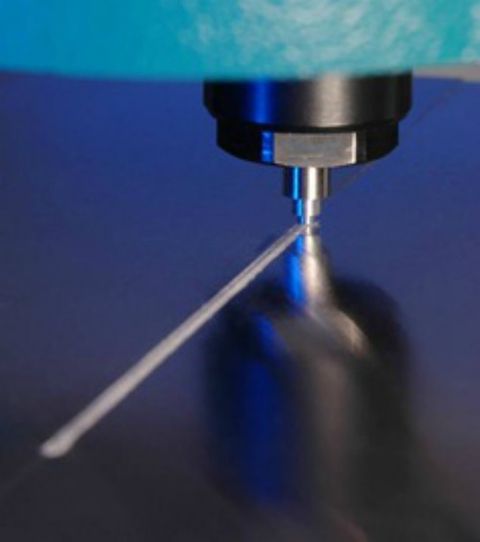
Making a Difference in Thermal Manufacturing
Our extensive experience in thermal friction stir welding solutions is evident in the enormous variety of parts our machines produce. Those applications include all types of custom heat sinks and cold plates. Friction stir welding plays an enormous role in thermal industry products. Friction stir welding machines produce reliable and consistent results in cold plates and heat sinks. Friction stir welding thermal products is more reliable than traditional methods. No leaking, improving aesthetics, providing strength, delivering cost savings – these are just a few of the many benefits friction welding produces in the thermal industry.
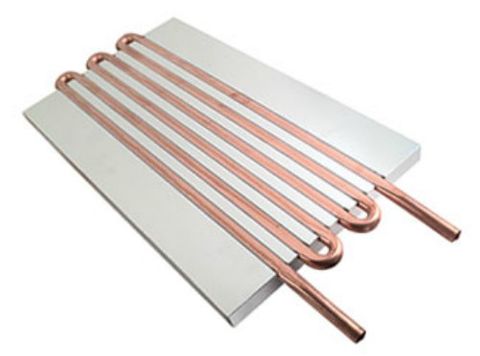
Why Friction Stir Welding is Vital for Thermal Applications
Friction Stir Welding not only adds new, improved weld strength and durability to thermal products but can significantly improve the product’s aesthetic quality while eliminating material and processing steps associated with arc based methods of welding. Friction stir welding tooling and techniques allow for the assembly of a complete product component at one time, and in just seconds, while generating minimal heat and few external areas to “clean up” machine to near net shape. Friction stir welding for the thermal industry allows us to make 100% leak free parts. Machining thermal products allows us to produce highly complex parts. Final products can use a minimalist design approach, coupled with a secure, durable, tamper resistant enclosure.
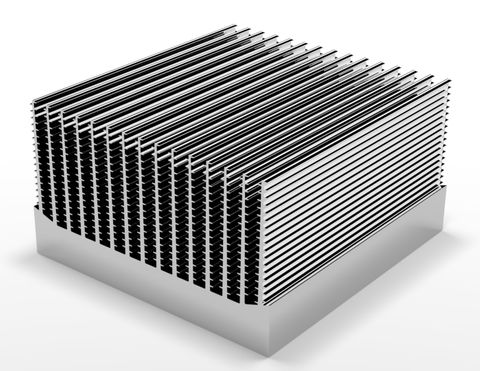
The Friction Stir Welding Process for the Thermal Industry can be Utilized to:
Hermetically seal cold plate type products and to join smaller, air cooled heat sinks together to produce a larger finished product. HFW can friction stir weld and manufacture:
- Cold Plates
- Heat Sinks
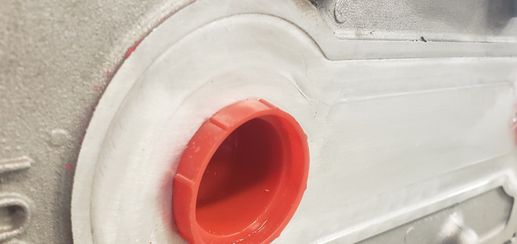
Aluminum FSW Casting to Extrusion
The Benefits of Using Friction Stir Welding for Cold Plate Assembly with Dissimilar Materials
Friction stir welding (FSW) is a solid-state joining process that can be used to weld dissimilar materials with different properties. In the case of manufacturing liquid cold plates, using a variety of materials in different parts of the welded assembly can have several potential advantages, including:
1
- Enhanced heat transfer: Different materials have different thermal properties, such as thermal conductivity and specific heat capacity. By using materials with high thermal conductivity in the areas where heat transfer is most critical, such as the cooling channels, and materials with lower thermal conductivity in areas where thermal insulation is desirable, such as the outer casing, it may be possible to enhance overall heat transfer performance of the liquid cold plate.
- Improved mechanical properties: Different materials have different mechanical properties, such as strength and ductility. By selecting materials with appropriate mechanical properties for different parts of the liquid cold plate, it may be possible to improve overall mechanical performance, such as resistance to vibration and fatigue.
- Cost savings: Using a variety of materials in the liquid cold plate can allow for more efficient use of materials, potentially resulting in cost savings. For example, high-performance materials can be used in critical areas, while lower-cost materials can be used in less critical areas. In addition, using castings, plate and extrusion alloys in targeted locations can optimize the cost depending on the requirements and quantity of the parts needed. (See photo)
- Customization: By using a variety of materials, it may be possible to customize the liquid cold plate to meet specific design requirements, such as weight reduction or corrosion resistance. This can result in a more optimized design and improved performance.
Overall, using a variety of materials in different parts of a friction stir welded liquid cold plate assembly can offer potential advantages in terms of enhanced heat transfer, improved mechanical properties, cost savings, and customization. However, careful consideration must be given to material selection and welding parameters to ensure that the different materials can be effectively joined together using FSW.
For a more in-depth discussion of Friction Stir Welding liquid cold plates and it's application in a production environment follow this link.